Based in Karlstad, Sweden, ShortLink SE develops low-power electronics for wireless communication and portable products. Among other things, the company designs custom mixed-signal and RF ASICs, along with offering radio and EMC testing. To design an ASIC with an IEEE® 802.15.4–compliant GFSK/OQPSK/PSK transceiver that facilitates communication between solar panels, ShortLink decided to use Model-Based Design with Simulink® and code generation instead of its former approach.
One reason for this decision was because standard-compliant and hardware-ready HDL blocks are already available in various MATLAB® and Simulink toolboxes. The team started with a floating-point model, which they converted to fixed point after the basic functions had been implemented. Although the engineers had never used code generation before, they quickly made the model buildable with HDL Coder™. Automatic code generation saved them an estimated six months of manual coding.
For verification, a testbench was created in Simulink with the two blocks for the analog RX front end and the digital RX baseband processing. After successfully running the testbench, the RTL and netlists for the ASIC were generated and simulated to verify that the digital parts of the hardware design behaved exactly like the Simulink model. Finally, the team verified the design on an FPGA to ensure that it also performed correctly on real hardware. With automatic code generation, they could be confident that no errors were introduced, and the finished ASIC design was then handed over to the chip manufacturer. ShortLink is also using this approach in another radio project currently underway.
Full article here.
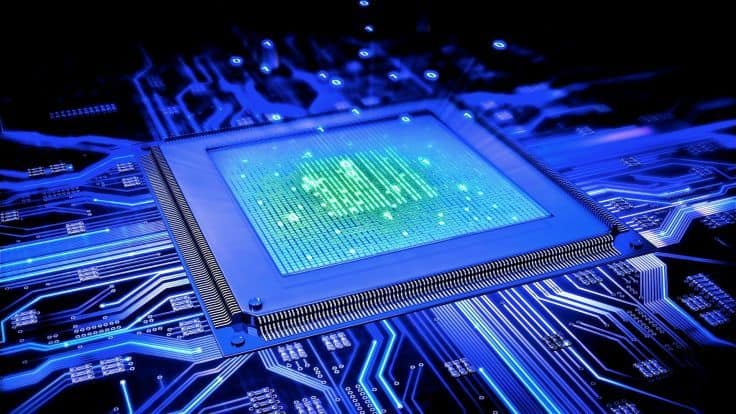
“The primary benefit of Model-Based Design is that it is fast and easy to set up a model in Simulink. Signals are readily visualized in the model with different tools. And because the RTL code can be generated, it is easy to test on an FPGA and see how the design performs on real hardware.”
– Jens Mellberg, ShortLink