The exponential cost of fixing EMC problems
EMC compliance is a crucial but often neglected part of the development of electronics. Approaching the EMC aspect of a product early in the design phase is the best way of mitigating the risk associated with EMC testing. Fixing EMC problems close to production is incredibly costly and risky.
This blog post discusses the exponential cost of fixing EMC issues and the value of early EMC testing.
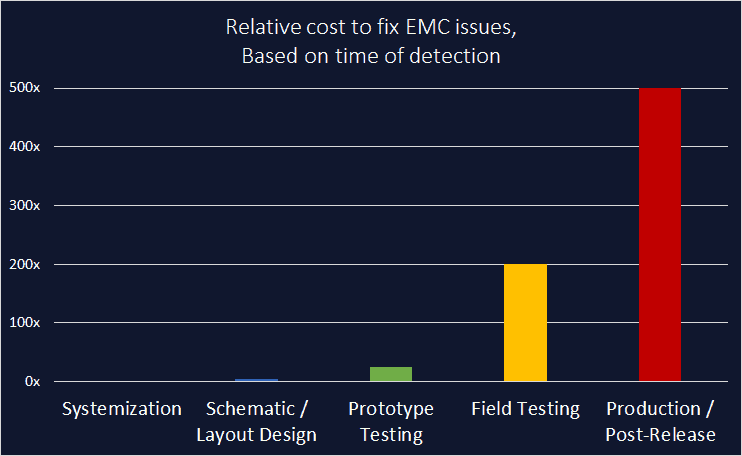
Worst case scenario: Fixing in production
Managing EMC by ignoring it
Many companies have a narrow view of the scope of EMC. It feels uncomfortable, a bit random, and unpredictable. But there is a clear acceptance criterion: pass the applicable standards (IEC / FCC) at an EMC compliance testing facility.
Without expertise in the field (heh) of EMC, the easy way out is to wait until the product is complete, cross your fingers and perform compliance testing on a production unit. If it works: great! If it doesn’t work: disaster. This is a direct application of the ostrich algorithm, which is bad risk management practice. The typical rate of first-pass success is less than 50%.
Non-compliance at the prototype stage is fine, suitable solutions can be tested and the design adapted to find low-cost solutions. Discovering it on a production unit puts immense pressure both on design mitigation and scheduling: EMC compliance can suddenly become your critical path to sales start.
Why is the impact so severe?
The cost of fixing EMC issues on a “finished” design is by far the most expensive and risky way. Depending on the circumstances it can be hundreds or even thousands of times more costly than fixing the problems earlier – if series production has started the sky is the limit.
What could have been a simple software fix or better planning of the circuit placement can now become expensive ferrite shields, custom metal structures, manual replacement of critical paths, or a large software rewrite. In the worst case, large reworks of the system can be needed adding months to the time plan, requiring extensive re-testing and re-qualification and the scrapping of any produced units.
What should you do?
Looking at the graph above, the solution is simple: Consider EMC aspects early in your design. There are many ways to achieve this, the two easiest ones are:
- Get an early review of the design. We offer EMC reviews of electronic designs at any stage of design completion. We can help you identify possible problem areas and suitable mitigation techniques to reduce the risk of EMC problems.
- Test as early as possible. Perform EMC testing as soon as possible, preferably as a part of your development process. Even a reduced test set can give you insights into problem areas to reduce the largest risks on your first prototypes. We can help you achieve the level of testing that is right during your entire development project, up to final compliance testing.
Take control of EMC with ShortLink Compliance
The next best thing to having your own EMC lab is to have a compliance testing partner during your development project. We offer this service along with many other testing services via our sister company ShortLink Compliance. We have extensive facilities, high-performance measurement equipment, and senior EMC design and measurement engineers.
Contact us to discuss how we can help you with your EMC and testing needs or read more about ShortLink Compliance.